As I delve deeper into this indigo-tinged world, I’ve been fortunate enough to meet and talk to many of the industry legends, pleasantly surprised each time at how unique, open, and friendly each of them has turned out to be. One name that would often come up during these talks was TCB’s Hajime Inoue. “Have you been to TCB yet?” I was often asked by other jeans makers. “You should go talk to Inoue-san” I was told. “He’s really friendly and he loves talking about jeans.” As synchronicity would have it (and this is a true story) the day before I was finally going to reach out to Inoue-san to see if he’d be up for an interview, I received a one-sentence message on Instagram from him that said, simply, “Hi. How are you?” I’ve no idea how he heard of me or found me (and I forgot to ask him during the interview) but needless to say we were set. I hopped in the car and did one of my favorite high-speed road trips: Osaka to Kojima. And I’m very glad I did.
As I crept slowly through the narrow streets of Kojima I couldn’t help but wonder if my navigation system had once again led me astray, as I didn’t seem to be anywhere near Jeans Street with only 100 meters to go until destination. I looked to be trapped in some retro-looking maze of streets next to a small river and yet technology was telling me I had arrived. I didn’t see anything in front of me but a rather normal-looking building. But there in the window among a display of ancient sewing machines was a small sign saying TCB. Sorry navigation system for ever doubting you.
Once inside, the building reveals itself as a jeans maker’s dream – full sewing factory on the first floor, stylish retail store on the second floor, fabric cutting done on the third floor. Inoue-san himself is exactly as advertised: friendly, open, knowledgeable, and very enthusiastic about all things denim. We spend the afternoon chatting away on his expansive covered balcony, talking Kojima, talking denim, laughing and eating a delicious curry that his wife brought by for us. A fantastic day it was, well worth the trip down from Osaka. Enjoy.
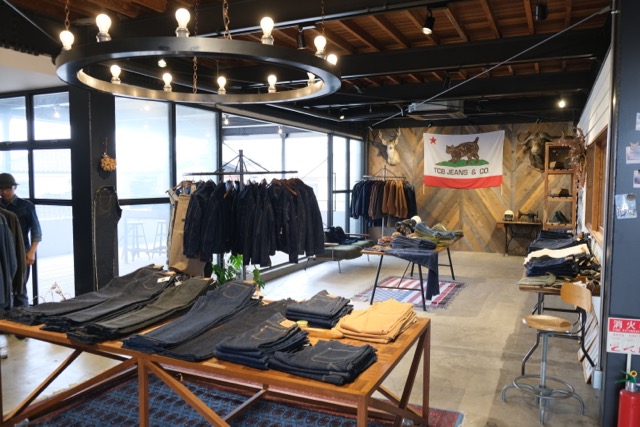
What were your original motivations and goals for creating your own denim company?
Back in the 90s when I was in junior high school, you know, I was finally at the age when you might be able to get enough money together to buy an item of clothing for yourself…but there was no internet back then, and I lived in the countryside, so I was like, “What should I even buy?” The only fashion information or advertising back then were magazines you know, that’s all we had. So I would look at them, and because it was right in the middle of the vintage American denim boom in Japan, jeans were featured pretty prominently, so I started to think that maybe that’s what I should buy. It wasn’t like jeans were a rare or mysterious thing back then; every guy my age was wearing them at that time.
Yeah I guess that would have been right smack in the middle of the whole denim revival here.
Yep, and every once in a while, amongst all the imported fashion denim stuff in those magazines, there would be something about jeans being made here in Japan. One small article said that these particular jeans came from Kojima, Okayama, and there was even a tiny little picture of the jeans factory. I still have that magazine. I had never really thought about it up until then, like where does denim or the jeans actually come from? I’m from Hiroshima, so when I read that article that said that people were actually making jeans in Okayama I was just blown away. But what was I going to do, realistically? I was only in junior high, so that feeling of awe and surprise faded quickly enough and it didn’t really enter my mind at that time that I myself actually wanted to make jeans.
Cool…but the seed was planted.
Yes. So for me the 90s went on, and my friends and I really got into all the vintage replica brands that were starting up. We’d try all the different ones we could, head down to the coin laundromat together to see what we could do with the fades and colors and all that. That was such a fun time for us.
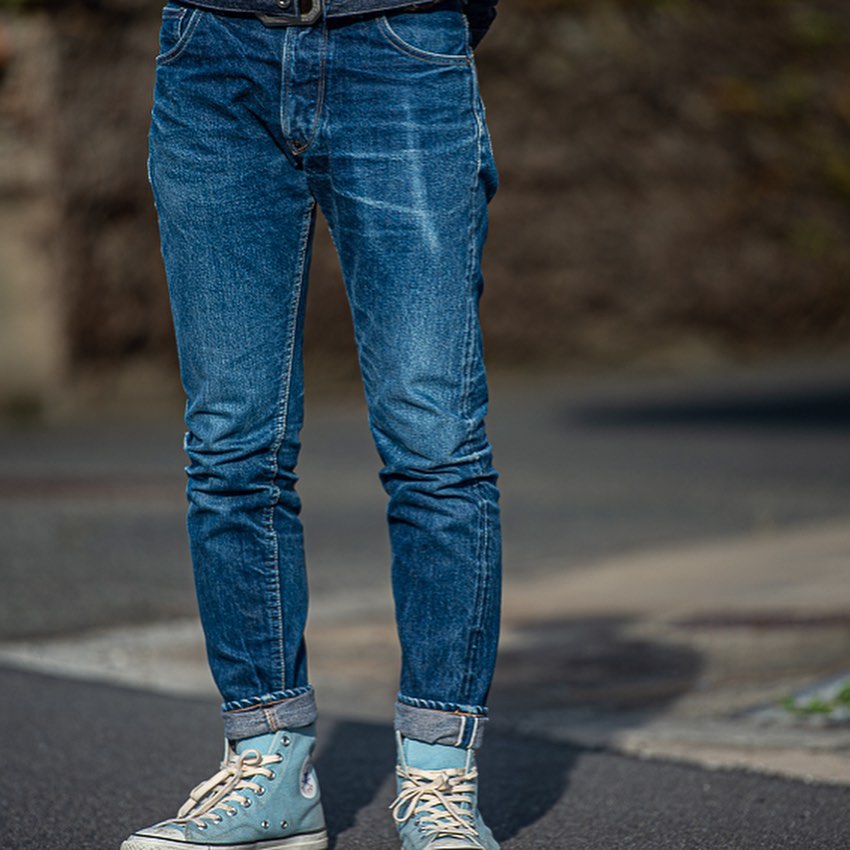
These are all Japanese brands you’re talking about now, right?
Yes, yes. In my generation we did have a longing for original American vintage stuff, but there was also the stuff now coming out of Japan. I think the generation before us was way more into the Americana thing though than we were, seeking out real vintage items and wanting to wear the actual old American stuff, even trying to take on the whole culture and feel of that era. So I don’t really know if we would have been called the second or third wave or what…I don’t really get all those designations but…yeah, that’s how we spent our teens.
Sounds alright.
It was. But then around the end of our teens, I had to start seriously considering what I was going to do with my life – where was I going to work? But looking back, I wasn’t really serious about finding a job at all. “What the heck should I do?” I would wonder. But the more I thought about it, the more I started to think that I wanted to do something with jeans…but actually making them still hadn’t occurred to me yet, so I figured that trying to sell them was what I’d do. As I said, I was in Hiroshima, and there wasn’t that much in the way of jeans shops back then so I headed north. I first tried to find something in Osaka, but it didn’t really work out. In the end, I was able to get a job selling jeans in Kyoto.
Kyoto? Wow. Interesting place to start. Can I ask you the name of the shop?
It was called Porky’s.
Is it still there?
Yep, it’s still there, though it’s changed. So I did that for a while not really knowing if what I was doing was a great job or not, you know? Yeah I was selling jeans, but I was also dealing in a customer service space where I was being asked about stuff like vintage looms, Union Specials, the craftsmen of Kojima, etc. Of course I got better and better at answering the questions that customers would ask, but I felt a growing discomfort about it too.
What do you mean?
Well, here I am talking about this stuff…explaining it as if I knew what I was talking about, as if I’d actually seen it. The only thing I’d actually seen myself was still that little magazine article I told you about earlier! I didn’t really have any hands-on experience or first-hand knowledge about what I was explaining to people – the mills, the machines, the craftsmen.
Ah, okay, I get it. Felt a bit fake.
Yeah, so I sort of sat down with myself and reconsidered what it was that I actually wanted to do with my life…and the honest answer was to make jeans, not just sell them. With this in mind, I went to my boss at that time and told him I was leaving, determined to go to Okayama. And so I came here. But when I arrived, you know, there was no internet. Well, I mean the internet existed but no jeans or sewing factories had home pages or anything like that, so what I ended up doing was just using the phone book. Back then there were still tons of pay phones around, each one of course having a phone book. So I just started at the top and called every kind of clothes or sewing place I could find. I called a lot of places. I’d just be like, “Hey, I’m 20, I have no experience, but can I have a job?”
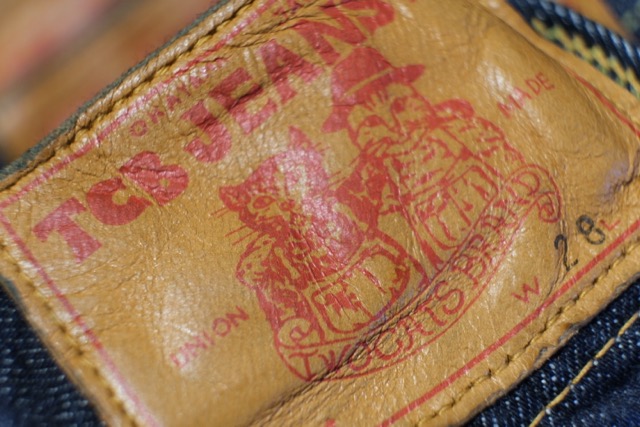
Ha, that’s awesome. I can picture it.
Kojima back then was known for making uniforms, school uniforms, so I called some of those kind of places. But they were like, “Sorry, we don’t need anybody with zero experience, and we don’t need any males for sewing anyway.” So I was a bit bummed when I heard all this. I had no idea that guys weren’t needed or wanted to run sewing machines.
Yeah, that would be pretty disheartening.
Luckily though, there was one single company that said that, if I was willing to study and learn, they could use somebody, not for sewing, but for maintaining and repairing the vinatage machines. It wasn’t exactly what I wanted to do, but I figured maybe it would be good to first just get into a company, any company, and then see what I could do from there. So I joined.
And how was it?
Well I did of course have the feeling like, “Aw man, what is this? This isn’t what I want to be doing…I just want to make jeans!” but looking back it was awesome experience. The factory I went into was actually the factory that sewed the jeans for…well, let’s just say a very famous American jeans company. The most famous actually. Through that work and study I came to learn how to fix, set up, and run all the old machines, the old Union Specials. Thinking back, it was the perfect education for what I ended up doing…so I’m actually really thankful that things went the way they did.
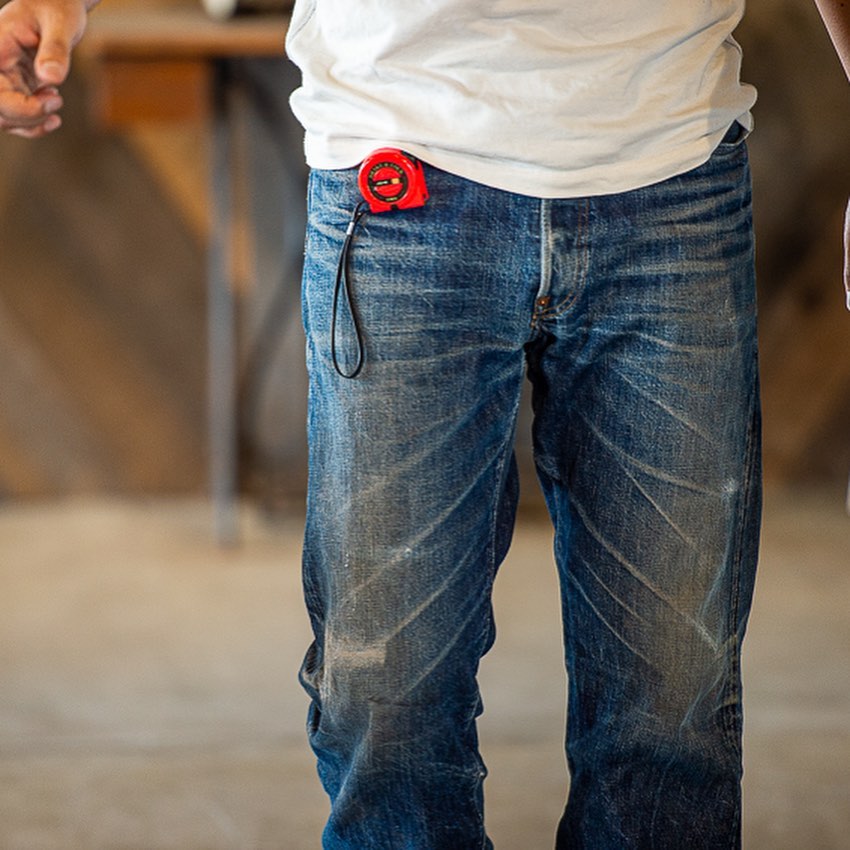
That’s fantastic. To have that hands-on experience with all the old models…
It was, now that I think back. After I’d been there just over a year, the famous American jeans brand I mentioned moved their production out of Japan and into somewhere else overseas and suddenly the occupancy rate of the factory dropped down to 60%, and we were suddenly in a position with nothing to do, no work. You know, then you’re stuck in that kind of job where you’re just kind of waiting, hoping maybe that business might come back. Once there are no orders coming in from the top down, you can’t do anything, you just grind to a halt. I was still young and didn’t want to be stuck in the position of having no control over what I was doing or whether work would be there for me or not, so I left.
I can totally understand that. What did you do then?
I became an organizer in kind of a trading company, working between designers, fabric mills, sewing factories. Like a salesman really…but I was actually thinking the whole time that I still wanted to use a sewing machine and make jeans. But as time passed, I actually started to enjoy the sales job I had because it connected me with so many different kinds of people. I also started to really get a feeling of what it would be like if I did become a jeans maker in the future…like these would be the kinds of people I’d be dealing with, these are the types of things I’d need to do, working with mills, factories, button makers, taking orders. Up until then I had only really known the inside of a sewing factory, but now I was like, “Whoa, there’s a lot to this”. I guess I was about 23 or 24 at this time.
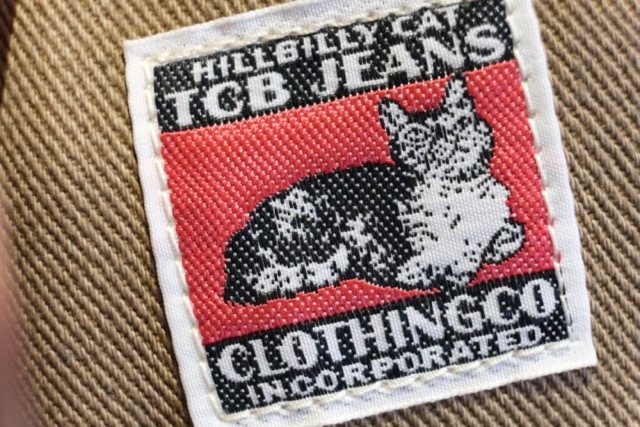
Still young. Were you happy to just carry on then as a salesman at that time?
As enjoyable as it was, I actually started thinking ahead and trying to imagine what the state of things would be ten years from then, when I was in my mid-30s and it really became obvious that sewing was going to become an issue pretty quickly in Japan. What I mean is that, even at that time, aside from maybe a few little specialist craft shops, all the people doing the sewing for the jeans companies I was involved with were in their sixties or over. So I was thinking that even if I did excel in my sales job and we started selling a lot of jeans or were able to drum up more customers, even if we did that, there would be nobody around to actually sew the jeans. We were going to be limited by that no matter what, so I figured that maybe that was where I should focus my energy and time – having a sewing factory.
So you could see the need even back then. Where did you go from there?
Well I think I was a bit lucky in a way in that when I told my bosses or those in my company that were older or more experienced in a way they…well they didn’t oppose the idea anyway! I don’t know if they thought it was the best idea they’d ever heard, but at the very least they weren’t against it. They knew my personality I guess too so they were probably like, “He’s gonna do it anyway so….” (laughs) Which is more than I could say for a lot of others at that time who were more like, “Are you seriously thinking of opening a sewing factory? Now?” On the surface maybe it didn’t make sense quite yet. I knew it would be hard, but I was thinking ten, fifteen years into the future and I really believed it would be needed in the long run. Plus it was what I had always wanted to do. I guess I was just young too. (laughs)
Okay, so we’re at 24 or so and you’ve just decided to open your own sewing factory.
Pretty much, but I didn’t have any machines of course at first. From then on I just used all of my monthly salary to buy old sewing machines. Not all at once of course, but I’d save and save, and then when I had enough money I’d get another Union Special, slowly building up an arsenal while still working in my other job.
Sorry, and this was all here in Kojima, right?
Yes, this was all in Kojima. So it took a while to get all the machines I needed because it takes at least 10 different machines just to make a pair of jeans, and when I finally had enough that I felt I could actually make a pair of jeans, I went totally independent. This was 2007.
Wow…that’s quite a journey, quite a story.
Yeah sorry, that was a super long answer to a single question (laughs).
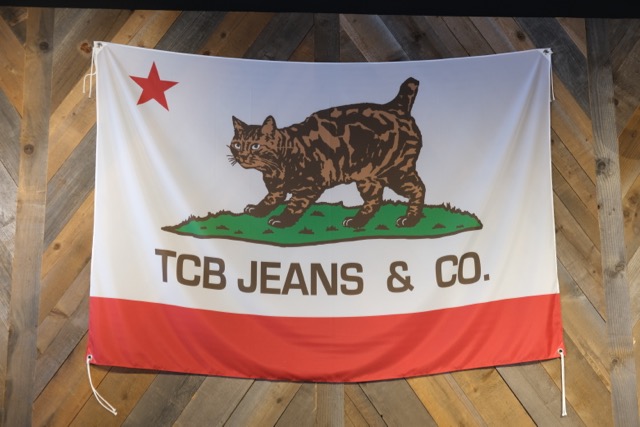
No, no, that’s great. Really interesting. What were some of the toughest obstacles or setbacks you had to face once you decided to go down the “my own sewing factory” route?
I knew for sure that I wanted to make things, but as far as exactly what I would make, or who I would try to work with, I had no idea at all. I loved using the sewing machine but there were so many choices on what to make, so I actually ended up doing subcontracting at first. But it’s like those impossible jobs where everyone is always like, “Hurry! When will it be done?” You can never do enough. I was young then though and that’s all I had ever really done up until then so I actually just thought that (kind of pressure) was normal. It was alright, but after a few months of that, one of my older friends I had worked with in the past came to me and said he wanted to do something together, work together. We eventually expanded to a group of five people but then I had to wonder about what exactly we wanted to make, who exactly did we want to work with, in what direction should we take this venture?
So you still weren’t making anything for yourself at this time, is that right?
We were mostly doing OEM work at that time, so of course we got work from our customers, but I really wanted to make truly good things, things of high quality, you know. I started to think that in order to do this I really had to consider who I was working with and working for. You know, there are all types of people out there. For some, cost is the main factor. “How cheaply can we do this?” is their primary concern, which is totally fine in a strict business kind of way, but I thought that that was one race I didn’t want to run in.
You just wanted to make the best things possible.
Yes. I decided I wanted to work with people who were serious about the quality of TCB, people who were thinking long-term. As we did this, I could slowly start to focus on making the things I felt good about making, I felt a kind of relief…a lot of those worries about what I was going to do, or if it would work, kind of started dropping away. But once I passed 30, I started thinking again about what my next step might be. Having my own sewing factory was great, but we were really just producing things that the preceding generation wanted to make. I wanted to make something of my own generation, otherwise I’d just be repeating the same thing into my 40s, 50s. I knew then that this would of course also involve selling my own stuff, not just making stuff for others.
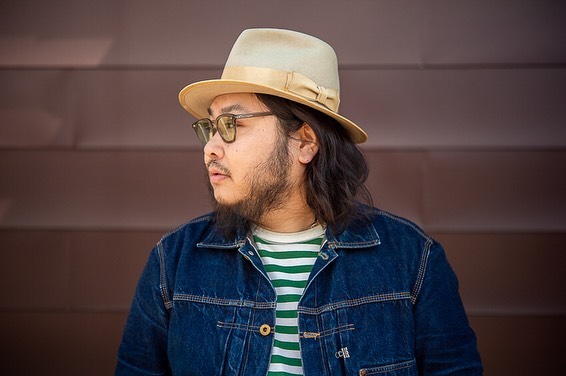
How did you get the word out about what you were trying to do?
At that time, Lighting was sponsoring a denim festival here in Kojima, a festival where jeans makers could show and sell their stuff, the Inazuma Festival. I had a friend from where I used to work who was involved in organizing it and they came to me and asked if I wanted to go in it. I of course replied that I didn’t really have any of my own stuff to show or sell and they were like, “Well you own a factory, don’t you? Why not make something??” (laughs) “Ah yeah…that’s true”, I replied, “I’ll try and make one cut of jeans in time for the festival.”
Do you still have those jeans?
Well we still make jeans of that style, but I don’t have any of the originals that we made, no. This might not sound very good, but all the companies kind of just discount their stock for this festival. It’s good for the customers of course, but for us at that time it was the first thing we’d ever made.
Were you happy with what you guys were able to make in such a short time?
Well more than thinking we had made something perfect, we were just like, “Yesss! We made something!” (laughs) In the end though we only sold three or four pairs at the festival, so considering all the work and planning it took to make them, we were definitely in the red.
Well yeah, only selling a few pairs you must have lost money.
We did. But more than wanting to sell stuff, the point of me going to that festival was more to show everybody that we had our own sewing factory. To that end, I actually brought a machine to the festival itself. I mean we had hardly any jeans at all to fill our booth with so I had to do something…so I brought a machine and used it in front of everybody and also let people try it. I think there were a lot of people who had never really seen that, and they were happy we brought that out to show everyone. There was a genuine interest and appreciation.
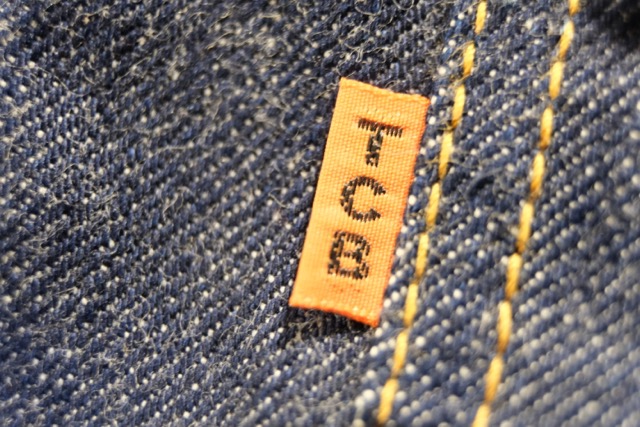
Interesting.
Really? (laughs)
Well it’s not your typical story so yeah, totally interesting!
(laughs) Well that’s good. So that was I guess the official launch of TCB as a jeans brand. This was 2012 so Facebook was already huge and we had a big reaction on there. I didn’t have money for advertising really, so it was SNS or nothing at that time. With that in mind I set out to post once a day about TCB…but of course the problem remained – what exactly to post? Sure, I could just dress up some attractive model in TCB clothes and post that everyday, but then are people really going to click on that because of the jeans themselves? I don’t think so! (laughs)
Yeah, no, probably not. (laughs)
Any brand can do that. I wanted to kind of have a unique theme, something that others weren’t doing (or couldn’t do) so I decided to focus on the making of jeans. I used the local landscape and the people involved in making the jeans in my posts, and I did that every day. There was a positive reaction to all of this, but not so much from inside Japan, but from overseas. People started liking and sharing the stuff we were posting and eventually introduced TCB on Superfuture, in a thread called something like “unknown Japanese brands”. They introduced us. We weren’t famous at all at that time, but people started to notice. We then decided to have a contest, people posting their fades, liking each others’ pictures, and that’s really how we began overseas. It came from the interest generated online, especially that Superfuture thread and contest.
So the first items you guys made, were those based on some existing designs or did you make them from scratch?
It’s like I was saying earlier, all those vintage and replica brands here in the 90s were doing their thing…all crazy about Americana, and I was the same. I still love that stuff. So rather than coming up with something from nothing back at the start, we also went with the feeling of those old jeans, particularly the stuff from the 50s. I’m not a designer at heart really, my roots have always been in sewing.
For new patterns, designs, ideas – are they from you or do you take cues from people around you?
My inspiration really comes from the clothes of the past. But it’s not always an exact replica…like if I want to make a certain kind of jacket I might get three vintage examples of the same type of jacket and then take certain elements from each that I like, put them together and come up with one jacket that’s a blend of those parts that I like.
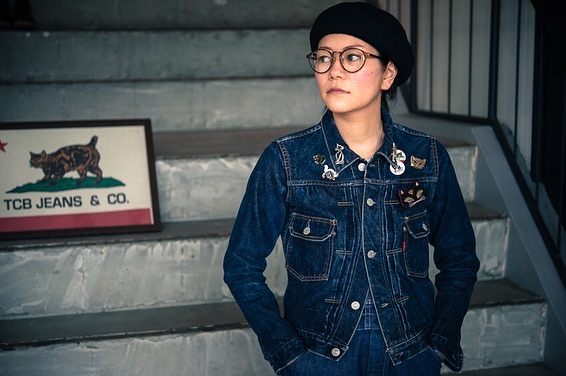
Are there times when customers’ requests might influence what you’re making?
I think so. Maybe not like a direct request, but just through many conversations with customers I get a feel for what people are wanting or not wanting. I really am grateful for that input and take it seriously.
I read online that TCB actually stands for two separate things, there’s two meanings.
That’s right, there’s actually two meanings.
Can you explain that a bit?
I was saying that we started with our sewing factory first. We called this company Taking Care of Business. I thought it was kind of cool slang and it sort of had meaning with what we were doing…doing what we had to do, and doing it as well as we could. Then when we actually started making our own stuff I was kind of like, “Well now what do I call this part of the business?” Nobody really knew the name TCB at that time so at first I thought I should come up with a whole new name, but as I thought more about it I started to think like, “Why not? The jeans are being made by TCB so why not just call them TCB jeans?”
Makes sense. So you went with that.
I did, and the double-meaning kind of came later. You’ve seen the old Levis ads where the two horses are trying to pull a pair jeans apart? There was one ad where they called them Two Horse Brand and it got me thinking. I had two cats at home (laughs) so I kind of thought Two Cats Brand could work, I thought it sounded good. So I kept the factory as Taking Care of Business while the jeans brand became Two Cats Brand, both conveniently sharing the same initials (laughs).
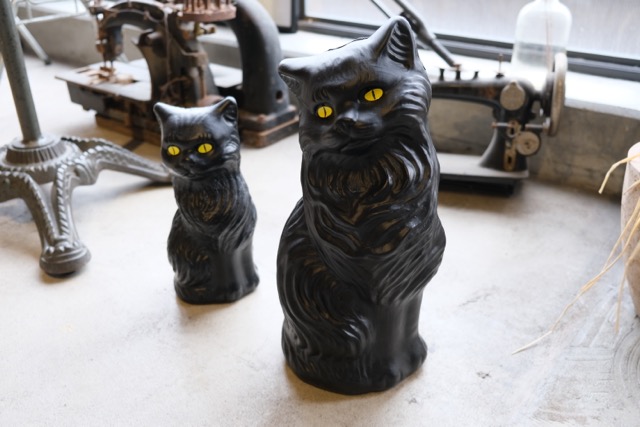
Are there any other Japanese jeans brands out there that you like?
Hmmm…yeah, to be honest, it’s a bit awkward for me to just start naming other brand names in response to that but…I like companies where people from the outside looking in can know about the people actually working there just by seeing the things they are making. There’s that connection, there’s a human touch that you can feel there. An “at home” kind of feeling, where people are into what they are doing. And it’s not just in clothing; lots of things are like that. Sure, there might be huge companies with famous names out there, but are the actual workers really connected with what’s going on? With what they are making or with their customers? I prefer the small companies where you can see the face of the makers. But yeah, to say exactly what other brands I like is pretty hard.
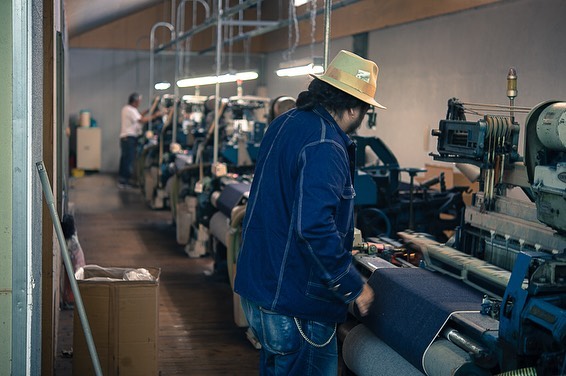
Can you say at least that you see the other brands as friends or as competition? Do you guys cooperate with each other?
For sure, for sure. We cooperate. We are all interested in denim, in jeans. Like with this interview, you’re interviewing me, so sure, if it increases interest in my company or people want to buy TCB jeans that’s great, but much more than that I’m just hoping that we can increase the number of people interested in Japan, in Japanese denim, not just this company or that company. I really want to spread the word about this area. You know, the population here in Japan is going down so fast…you’re in Osaka so maybe you don’t feel it as much, or maybe in Tokyo it doesn’t seem like it’s happening, but overall it’s a really serious problem for us in Japan.
Yeah you can really notice it once you get out of the city.
So it’s more like we’re all doing our best to support this area itself, like letting people overseas know, like, “Hey there’s this area like this…and we make things like this…” That’s what we need to do. There’s really no room for selfishness in this kind of situation, like, “Hey, just look at my company” or something like that. So if even one person comes to Kojima because of this interview I’ll be happy…and they can totally head down to Jeans Street and buy a different brand (laughs). I would be happy just to increase the interest in the area, in Japanese denim.
You’re a good man (laughs)
That’s not to say that there isn’t any competition at all between us – there is. But it’s a good type, a fun type. There’s no need to pull somebody else down and try to crawl over them to get ahead. It’s all good.
How many overseas customers would you get coming in here to the actual shop?
It depends on the season but around now, in the fall, it might be 10 in a month.
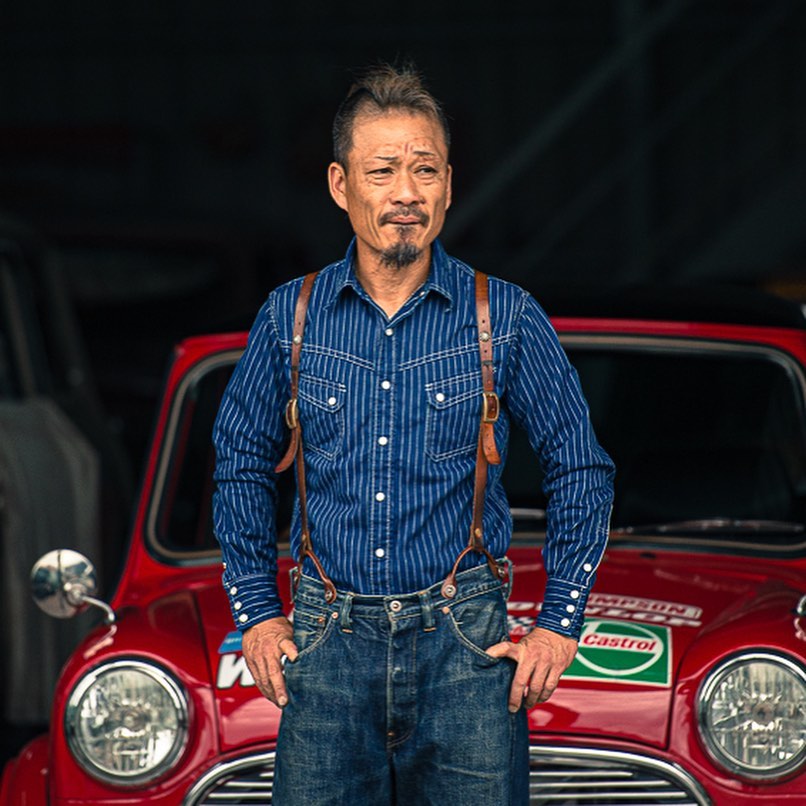
How is the average customer from overseas different from the average Japanese customer?
Overseas customers kind of remind me of Japanese denim fans back in the 90s, super interested and supportive. That’s so fun for me actually. For Japanese customers these days, there’s kind of two groups, one being of course the generation just before mine where everyone has been wearing denim since the 90s, and still are into it. This is the base, but I also think that what we need to be doing is making a new generation of jeans fans. Like right now when a lot of younger Japanese people come in and I’m like, “This raw denim you’re buying will eventually look like this” and then I show then some faded samples, they are really blown away. They didn’t know raw denim did that.
Really? That’s kind of surprising actually.
A lot of them never even thought of that part of it, they just assumed the jeans would stay the same dark color forever…it didn’t even enter their minds that these jeans are going to change and fade. So I really think it’s important to impart this sense of interest in the generation of today by showing them fade samples and letting them know that that’s what raw denim does – it changes according to wear and the wearer. That’s a huge part of the fun. In my opinion, I think there might be a bit too much emphasis just on trying to get stuff sold these days, whereas we should be focusing just as much on teaching, transferring information to customers, creating interest. This is really my main mission heading forward.
What’s the best part of your job?
Like our meeting today, the best part about making jeans for me is all the people from around the world I get to be in contact with. If I hadn’t started making jeans, there’s no way I would have been able to meet so many different kinds of people so…yeah, that’s the best part about it for me. Connecting people around the world. Sure, the business side of it is also important, making sure you can sell what you make provides its own motivation, but for companies that just focus only on profits…especially in making clothes, I just don’t see how they can continue forever. You can’t make that the one and only driving force. For me, the past 12 years has been really about the people I’ve been able to come in contact with.
What’s the toughest part?
(thinks for a long time) I think it’s ‘crafting a craftsman’ so to speak. Being a true craftsman isn’t not an easy thing, nor is it easy to take a young person and raise and train them to be one. This would be the hardest thing.
What’s your personality like?
Personality? My own? I’m a nice guy! (laughs) But seriously…personality…that’s a tough one…
(laughs) Sorry, sorry…
No, no, it’s fine. I’ve seriously never really thought about it before. People do say that I’m pretty set in what I like, meaning that I’m really into things that I like. I’ll really take care of those things that are important to me, but if I’m not into something or it’s not important to me…then…yeah, not so much.
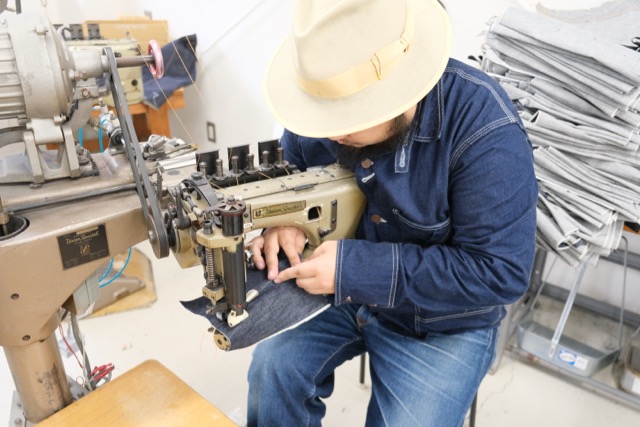
This is connected, but what do you like outside of work? What makes you happy?
What’s work and what’s not work is so blurred for me. Like coming in to work here every day I don’t really see it as work, and when I go home at night I’m still thinking about jeans so…it’s hard to tell what’s actually my ‘work life’ and what’s not. But I do love taking pictures, photography, especially of people.
What’s your hope for TCB in the future? Do you have any kids who might want to take over?
I just had a daughter last year. Of course I want TCB to be successful in the future as far as the business end of it goes, but whether or not my daughter will eventually take over or not, that would be her decision…and that’s a long ways off (laughs). She’ll have her own generation and I’d like her to do something she’s interested in.
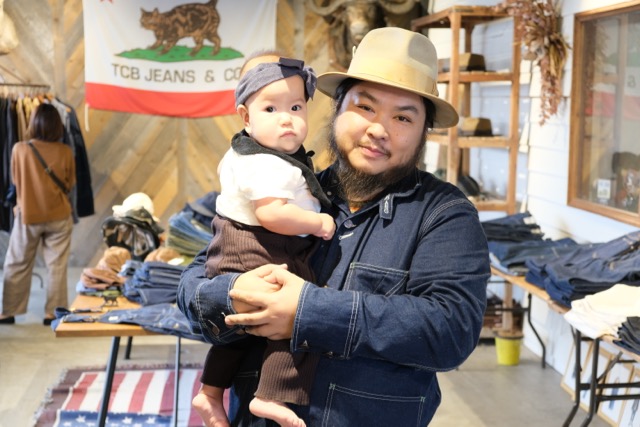
Do have any favorite model of jeans or fabric that you’ve made so far?
Since the start I’ve making different fabrics based on vintage Levis stuff, but just this year we’ve also started doing fabric based on vintage Lee jeans, so that’s been really exciting. It’s just an awesome color (shows me a sample).
How was it being in that denim documentary that came out a few years ago, Weaving Shibusa? I’ve seen that so many times now.
It was good. I was just saying the same thing I’m saying now, that we need to find a way to survive into the future, my feeling hasn’t changed on that. I also went in that movie because I wanted people to learn about making jeans, get them interested in coming to Kojima. Remember I was telling you about that little ad in the magazine way back in the 90s? That’s what got me interested in all of this. I want to ‘pay that back’ in a way…like inspire others to get into jeans just like I was inspired. Like if I knew that somebody read this interview we are doing now, and then in 20 years I hear that that person is now somewhere in the world making jeans because of what they read…that would be just awesome. It’s like a perfect romantic story.
Just going back to fabric for a minute, are you always making the same basic types or are you constantly experimenting with the mills?
Well, as the number of things we make increases, so will the types of fabric we need, so yes there is a lot of development that goes on. But we don’t use a different fabric for every single item. Some various items will be based on stuff from the 50s and so we’ll use our 50s fabric for those. But of course it’s not enough just to dream up some new fabric you want to make – this then needs to be translated exactly to the mills and you hope they can make what you have in your mind.
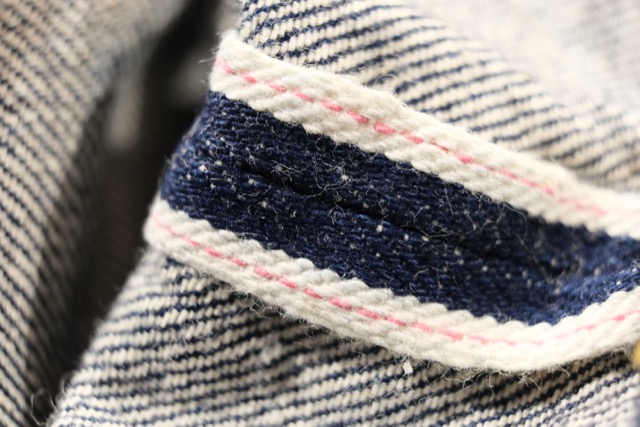
How many mills do you use?
Basically two main ones. Both in Ibara (Okayama).
Do you think there is going to be a shortage of selvedge denim in the future?
It’s an issue for sure. Firstly, all the looms are antiques so…they’re not making any more of them. Secondly, the people who can fix and maintain them are decreasing as well, so at the very least there’s no way that we’re going to be making more denim in the future than we are able to make now.
As far as sewing goes, you do all of yours right here?
Yes, we do.
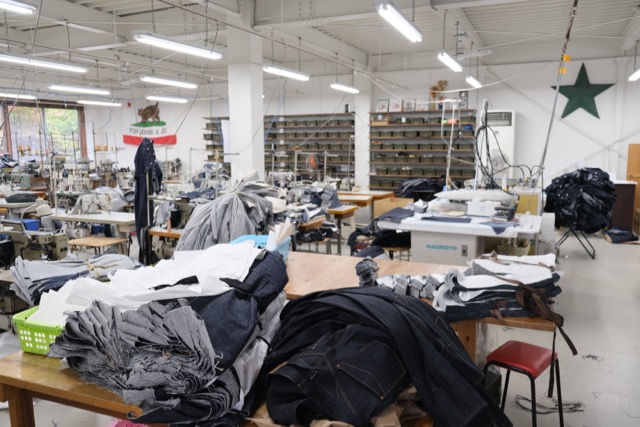
What do you do when customers come in that can’t speak any Japanese?
I just do my best to communicate with them. When it comes to basic stuff like sales or talking about jeans, I can get by. I don’t try to be perfect about it. For me, rather than trying not to make any mistakes, I think the important thing is just to give it a go, you know, do your best. Communication is kind of like playing catch with somebody, that back-and-forth. I probably say a lot of stuff wrong, and there are things I just can’t express, but overall, for people coming here, they’re interested in jeans so I can get by somehow on those kind of topics. For harder stuff, there’s always Google Translate too so…we get by somehow.
Are you interested at all in heavy or slubby denim? Do you ever feel like making some yourself?
Well, TCB is really about creating stuff with a vintage feel so…stuff like you’re talking about takes a special way of making so I can’t really see doing it at the moment within our brand. I know that there are some kind of slubby fabrics that, when people overseas see it, they feel like it’s pretty cool, like old-style Japanese traditional clothes, so I could see maybe doing some kind of exclusive item in a fabric like that, but overall, not for any of our main stuff.
Lastly, all of your stuff is made from Zimbabwe cotton, right?
No, no, not all…not all of it. I did first start out using only Zimbabwe cotton, but now I use several different types.
So do you use Zimbabwe cotton at all now?
Yes, we do. Do you want to see some more fabric? (goes and gets rolls of labeled fabrics) These are some of our fabrics. So our 50s fabric is like the Levis stuff from the 50s. Our Cowboy fabric is like Lee. The thread colors are all different, as is the weight, even the rate and way in which each fabric fades is different. Like these Levis have indigo going one way while the warp is left natural, undyed. With the Lee fabric that thread is actually grey. Can you see it?
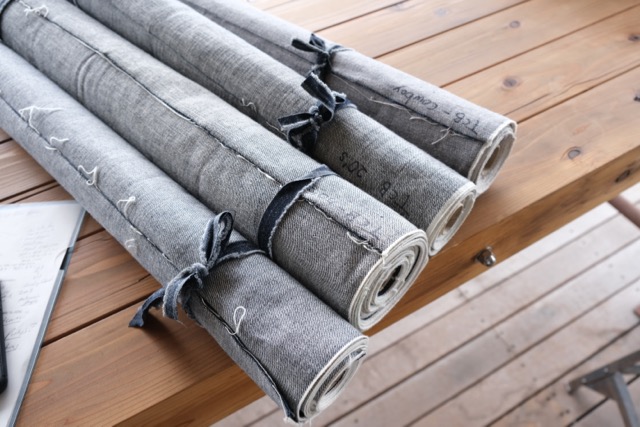
Oh yeah, I can totally see the difference.
So for the Lee fabric we dye the warp and the weft.
What is this stuff?
That’s our 20s fabric, like that from the 1920s. It’s about 12.5 oz. And this is our 60s fabric…when jeans started to become ‘fashion’…really blue. So we make our fabric with the image of each decade or time period in mind, we want to convey that feeling.
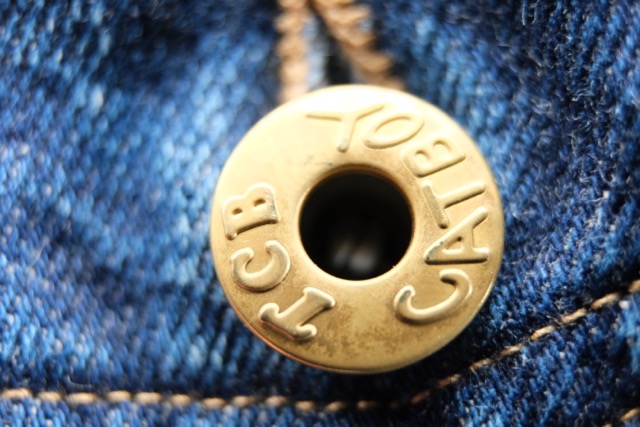
Lastly, do you have anything you’d like to say to the TCB fans (or just denim fans in general) who will be reading this interview?
Like I was saying, the best part about doing this is all the awesome people I get to meet, and so to continue that, I am going to continue making the best stuff I can for people to love and enjoy. That’s about it.
This has been great Inoue-san, thank you so much for today. People will love learning more about you and about TCB.
Really? If so, that’s great. Thank you for doing this too.
My pleasure. I’m just going to have a look around the shop, take some pictures if that’s okay.
Absolutely. Take your time and then we’ll head down to the sewing factory and I’ll show you some stuff.
Sounds great.
Quick TCB brand bio here.
TCB homepage here.
Hi,can i provide u my exact lenght to measure,how to i sent u picture of my lenght
As i like yr model TCB 20’s jeans/ one wash,can i knw the lenght
Pingback: TCB Jeans, The "Two Cats Brand" - History, Philosophy, Iconic Products
What an amazing interview. Reading this I just want to quit my day job and invest all my saved up money in all the machines needed to make Jeans and just go for it! Thanks for telling the story of your life Inoue-san!
Really interesting interview Dave! Well done and thank you Inoue-San for sharing. I’ve yet to own something from them but it won’t be long. Something that really intrigued me is their fabrics, designs and the team behind it. The thing Inoue-San said about finding a connection to a brand and the people behind it is something I really value too, and that’s something TCB themselves are very good at!
Really great interview. I have a few TCB items and they are fantastic. The passion and authenticity of Hajime Inoue shines through!